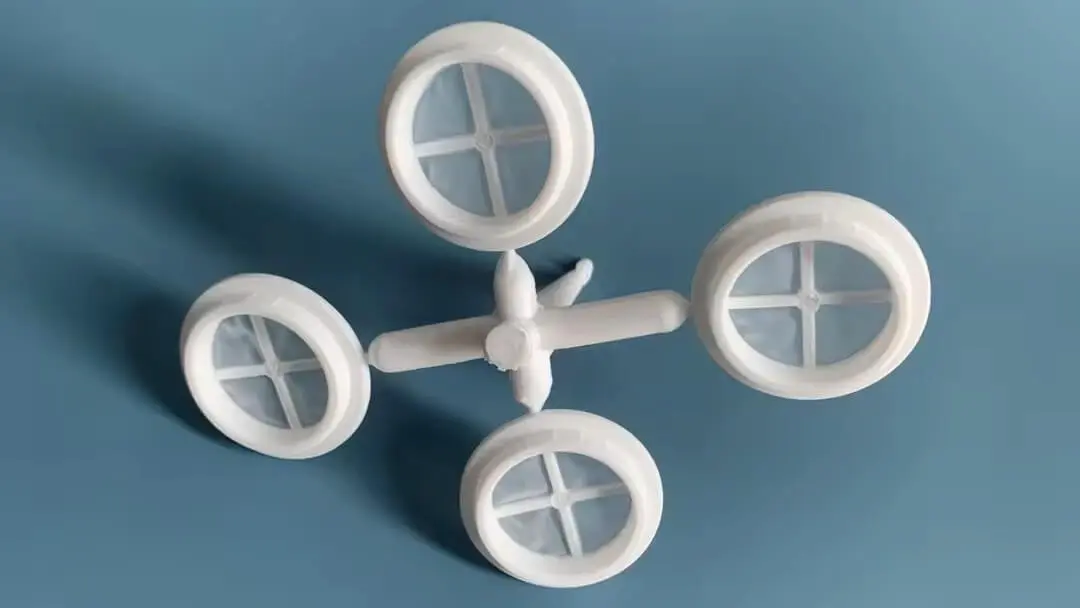
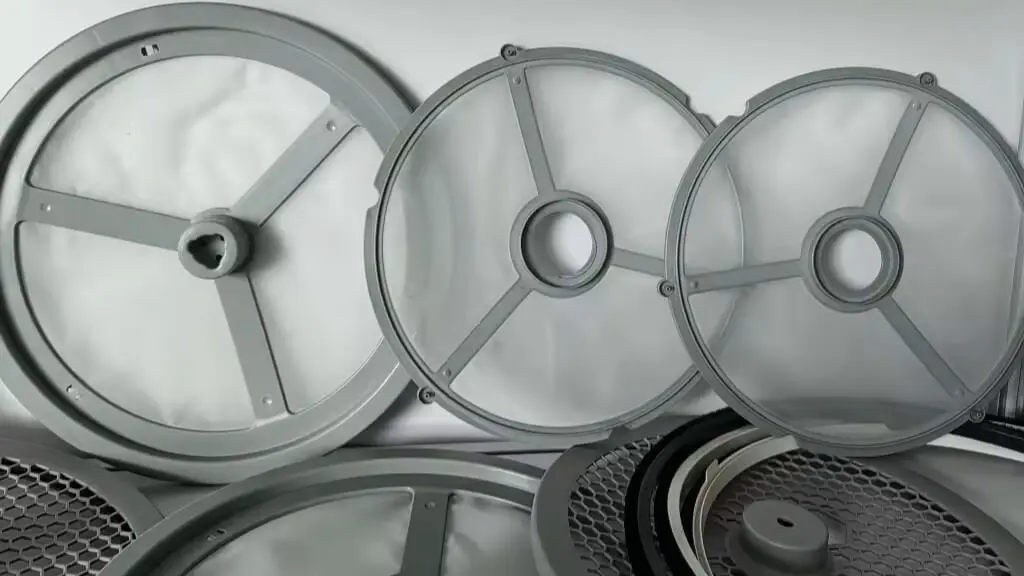
メッシュ・インサート成形とは
プラスチックにメッシュを一体化し、 高強度・高精度パーツを実現する成形技術
国産メッシュ・メーカー 株式会社
メッシュ・インサート成形の プロセス
- メッシュをセット
- 樹脂を射出
- 一体化&成形完了
メッシュ・インサート成形の メリット
- 軽量化
- 強度向上
- 高寸法精度
メッシュ・インサート成形の 代表事例
- 自動車部品
- 電子機器
- 医療機器
メッシュ・インサート成形の メリット
高い強度と耐久性
メッシュ状のインサートを組み込むことで、接合部分の強度が向上し、耐摩耗性や耐衝撃性が向上。
軽量化
金属や他の素材を部分的に埋め込むことで、全体の重量を抑えることができ、軽量化に寄与。
複合素材の一体成型
異なる素材を一体化できるため、機能性や性能を向上させることが可能。
コスト削減
従来の組み立て工程に比べて、成型一体化により組立コストや工程数を削減できる。
デザインの自由度
複雑な形状や細かなディテールを一体成型できるため、デザインの自由度が高まる。
耐腐食性・耐候性
適切な素材選定により、腐食や劣化に強い製品を作ることが可能。
高い再現性と安定性
大量生産においても、均一な品質を維持しやすい。
メッシュ・インサート成形の デメリットと対策
金型コスト・納期
- デメリット
- メッシュや金属インサートを確実に固定できる複雑な金型設計が必要なため、試作〜量産までの初期投資が大きく、通常射出成型に比べ成型サイクルが長くなる。
- 対策
-
- 部品のモジュール化・共通化、CAE解析、ミニ金型トライで金型トライコストと時間を削減
- インサート自動供給装置とロボットハンドリングで投入時間を短縮
- 冷却チャネル設計最適化と複数キャビティ金型の採用によりサイクルタイムを短縮
シビアな成型条件管理
- デメリット
- 樹脂の流動性・温度・圧力・冷却バランスがわずかにずれるだけで、メッシュずれや充填不足を起こしやすい。
- 対策
-
- 成型シミュレーションによる前解析で最適パラメータを設定
- デジタル温度・圧力センサーとPLCによる自動フィードバック制御
- 初期ロットでの詳細パラメータ表を作成・管理し、作業標準書を徹底
品質リスクの増大
- デメリット
- メッシュ浮き、樹脂密着不良、反り変形などで不良率が高まりやすい。また、インサートが内部に埋没するため外観検査だけでは欠陥を検知しにくい
- 対策
-
- メッシュ表面にプライマー処理や射出用コーティングで密着性向上
- 成型後サンプルにX線CTや超音波検査を実施し、SPC(統計的工程管理)で傾向管理
- インラインカメラ + AI画像検査を併用して、早期に異常兆候を補足
リサイクル性の低下
- デメリット
- 金属メッシュと樹脂が一体化しているため、製品解体時の分離が困難でリサイクルコストが増加。
- 対策
-
- 分離性を考慮した「着脱可能インサート」や溶融分離可能樹脂の採用
- 製造ラインにおける使用済み製品リサイクルループ(自社回収・再粉砕)を構築
- リサイクル性を高めるため、代替材料(ECO樹脂 + 高強度繊維)を検討
メッシュ・インサート成形の 適用分野
メッシュ・インサート成形は、異物除去から補強まで、軽量かつ高耐久が求められる各種産業の部品に幅広く応用されています。
自動車用流体フィルター
燃料ラインやATFラインなど、マイクロ異物の混入が許されない油圧・燃料回路に採用。樹脂ハウジングとメッシュを一体成形することで漏れゼロ・高耐圧を実現し、軽量化と部品点数削減によるコストダウンに寄与します。
医療機器用薬液ストレーナー
透析装置や点滴ルートなどの薬液フィルターに最適。メッシュと医療グレード樹脂をクリーン環境下で一体化することで溶出成分の低減と高い寸法安定性を両立します。
家電・小型モーターの防塵スクリーン
掃除機やドライヤーなどのエアインテークに使用。問題となりやすいメッシュの浮きや振動騒音を樹脂リブで固定して解消し、メンテナンス交換もワンタッチ化できます。
農業・散水ノズル内蔵フィルター
散布液中の異物詰まりを防ぐストレーナーをノズル本体にインサート。ねじ込み継手を省略でき、現場での分解清掃工数を大幅に削減します。
鉄道・航空向け軽量補強パネル
CFRP・GFRPパネルにメッシュを局所的に埋め込みリブレスでも高剛性なハニカム構造を実現。防火規格を満たしつつ10%以上の軽量化を達成した実績があります。
IoTセンサー用マイクロメッシュキャップ
湿度・ガスセンサーを外気にさらしながら異物侵入を防ぐキャップに採用。φ0.1mm以下のメッシュを歪みなく封入できモールド後でも通気抵抗のバラつきを±5%以内に抑制します。
tantoreの メッシュ・インサート成形
過去の実績からメッシュを様々な形状に加工が可能。
高度なメッシュ・インサート加工もすべて社内の技術で完結。
tantoreのメッシュインサート成形技術
- 絞り加工
- 超音波溶着加工
- 熱溶着加工
- トムスン抜き加工
- スポット溶接加工
- ヒートカット
- 縫製加工
メッシュインサート成形の写真ギャラリー
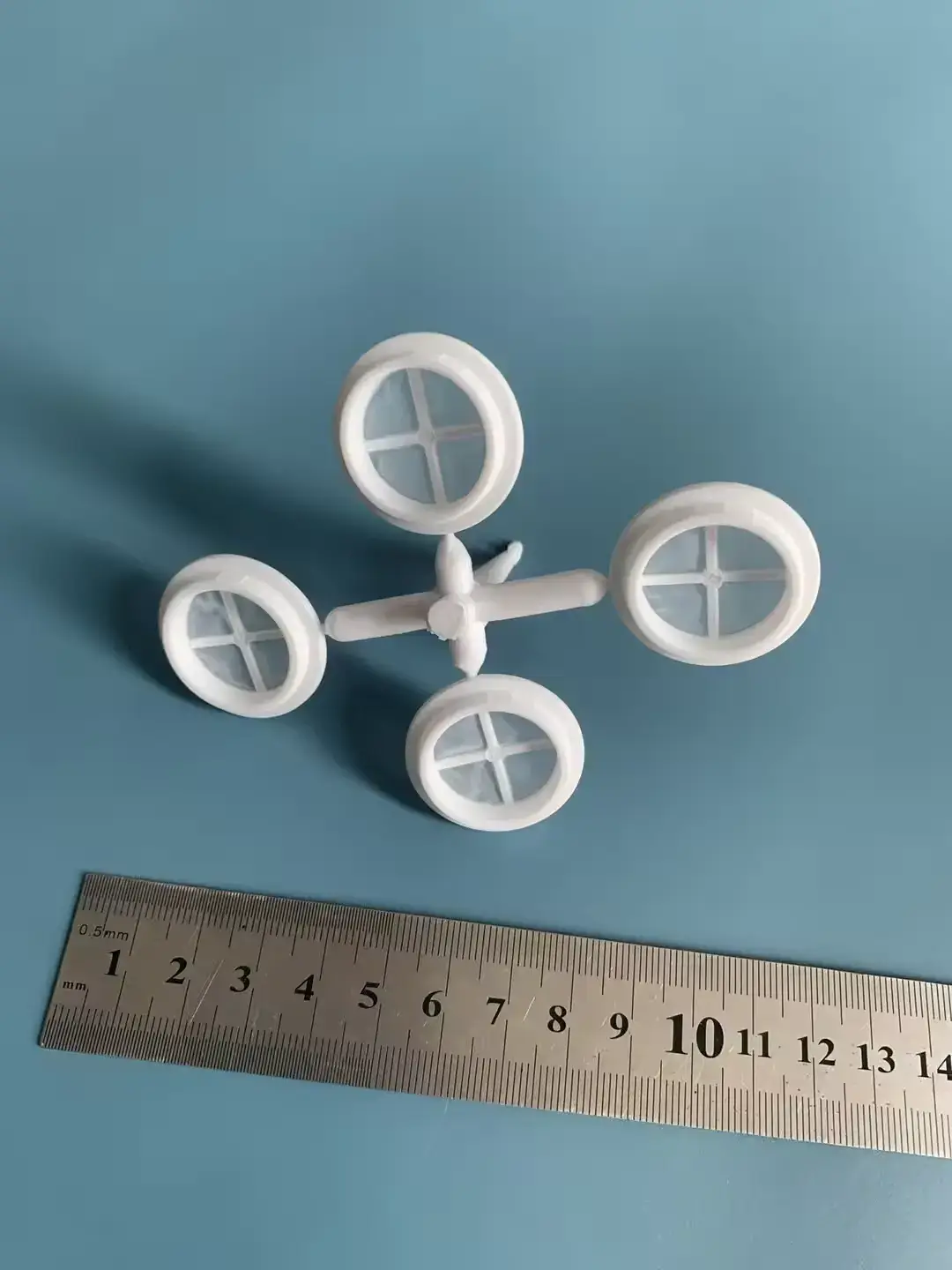
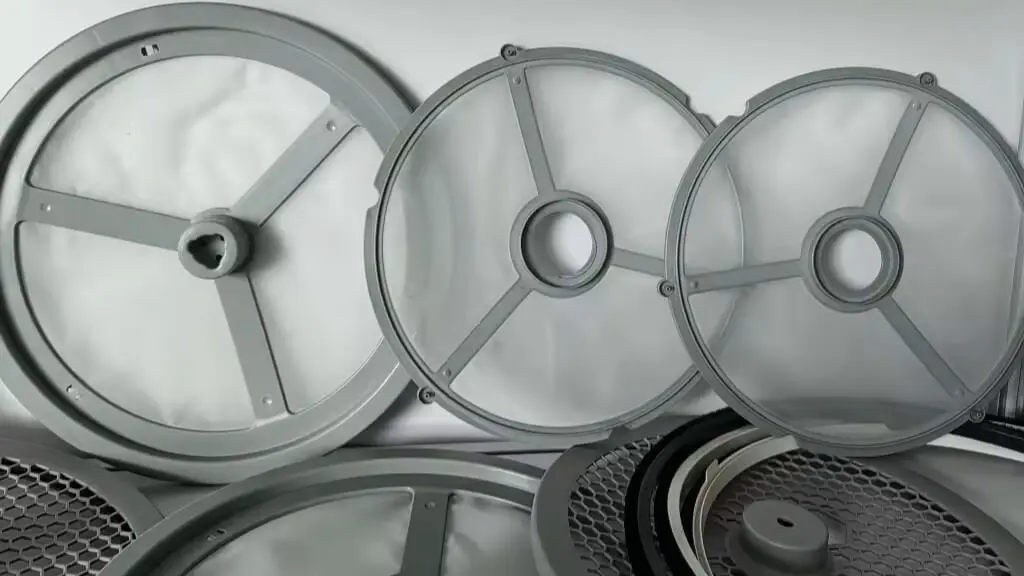
メッシュインサート成形 よくある質問
弊社では、3.5メッシュから1500メッシュの超高精度ナノメッシュまで、幅広いメッシュに対応しております。独自の射出条件・金型設計で高精度に一体成形が可能です。
試作は約2〜3週間、量産は金型製作後、約4〜6週間程度で立ち上げ可能です。短納期での対応もご相談ください。
材料や金型仕様によりますが、量産品は1,000個〜、試作・評価用は10〜50個から承ります。
ナイロン、ポリエステル、ステンレス、鋼、銅など、耐熱性・耐薬品性を考慮した各種金属・樹脂メッシュに対応。レアメタル・メッシュも取り扱っております。用途に最適な素材をご提案可能です。
金型設計費 + 射出成形費 + メッシュ材料費で算出します。試作で30万円〜、量産では1個あたり数十円〜数百円が目安です。まずは無料見積りをご利用ください。
当社のインライン検査と統計的工程管理により、±0.1mm以内の寸法許容差を維持。X線CT検査等を通じて高い品質を保証します。
図面データ(PDF/DWG)、メッシュ種類・メッシュサイズ、数量、使用環境(温度・耐薬品性)をお知らせください。仕様に沿って最適なメッシュもご提案可能です。ご不明点はお電話でもサポートいたします。
メッシュインサート成形 今すぐお見積もり
通常3営業日以内にご返信 お気軽にご相談ください。
- TEL
- 0532-37-1157
- FAX
- 0532-37-6023
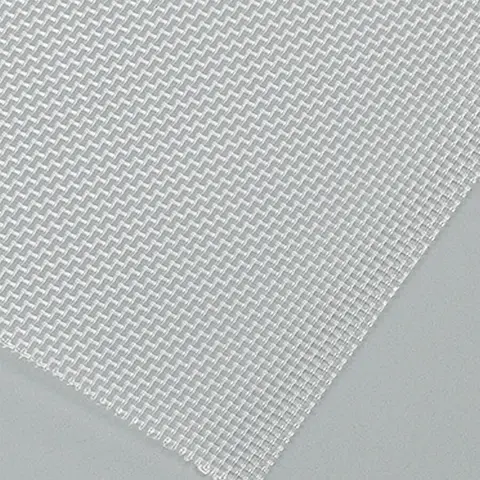
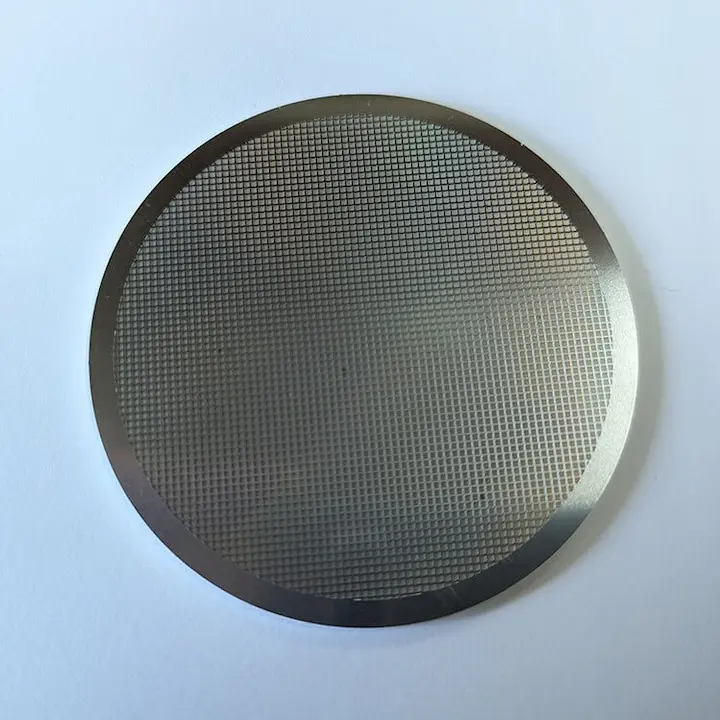
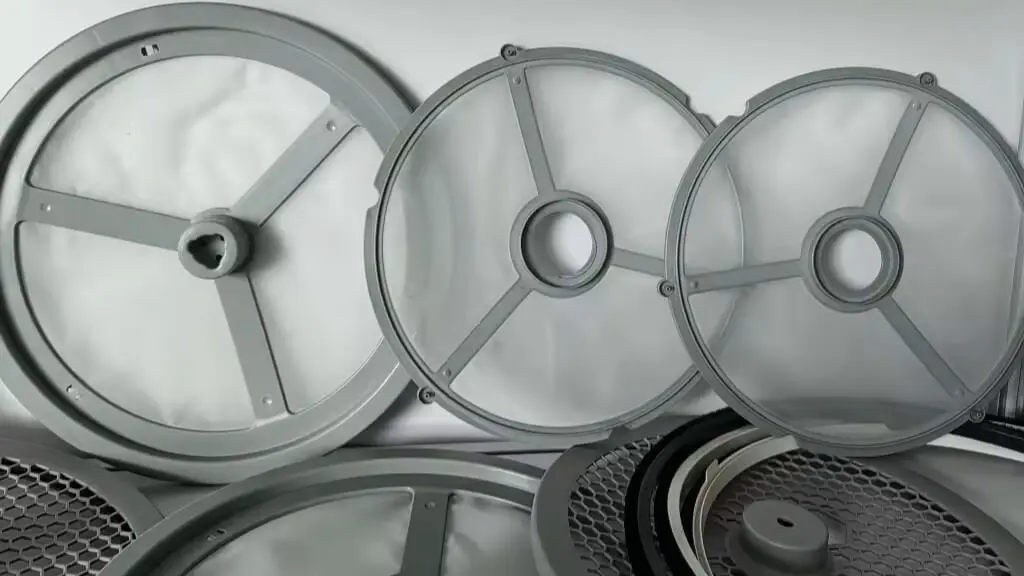

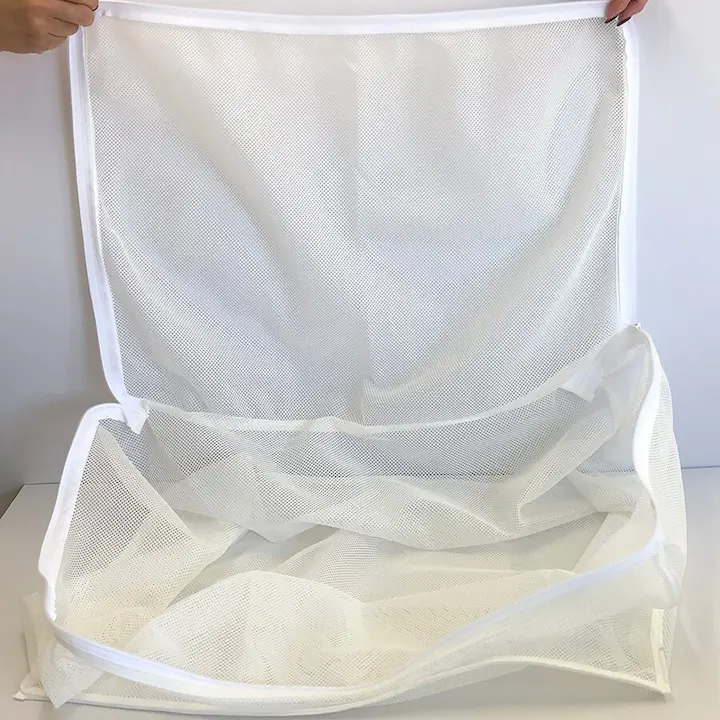
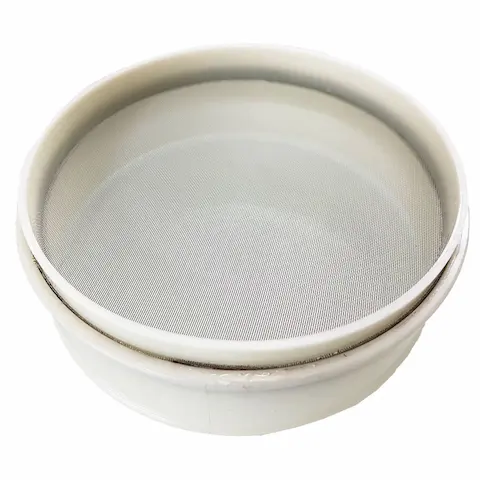
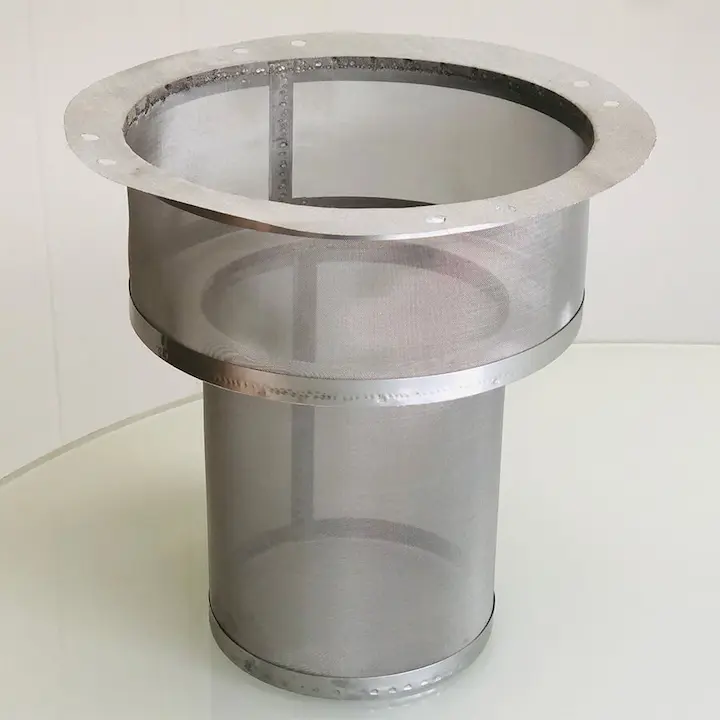
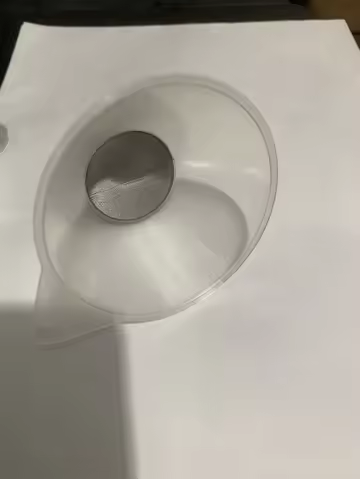
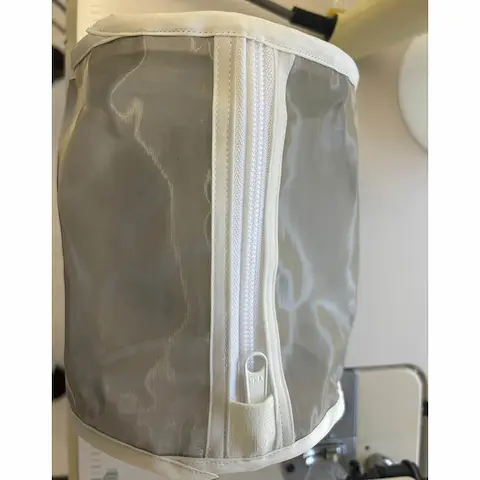
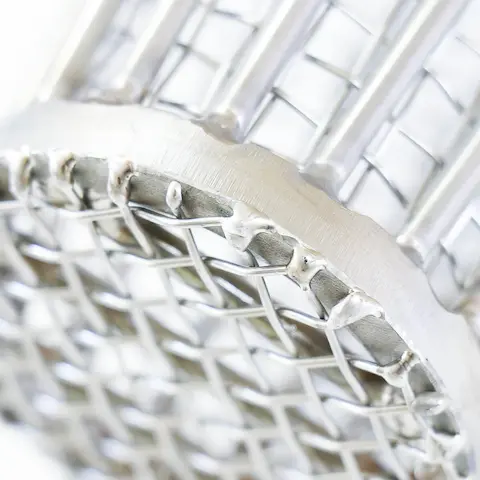

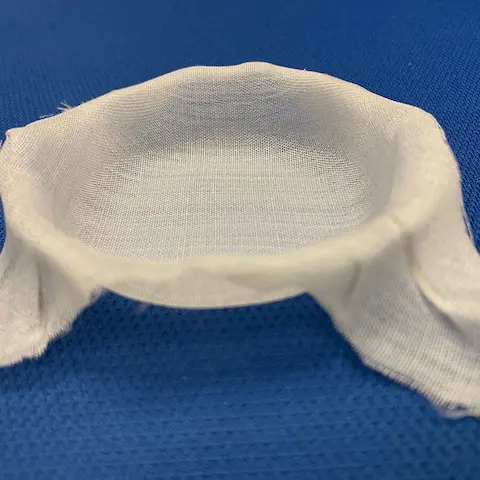

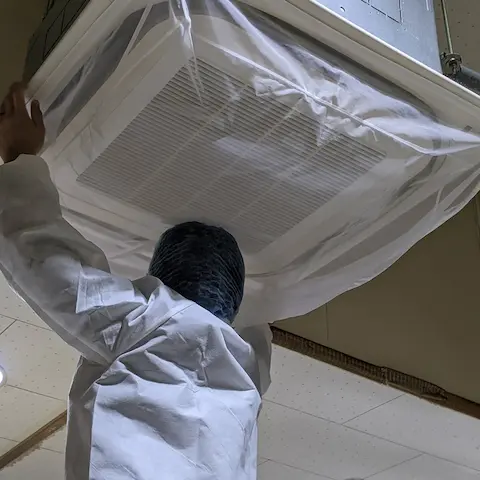
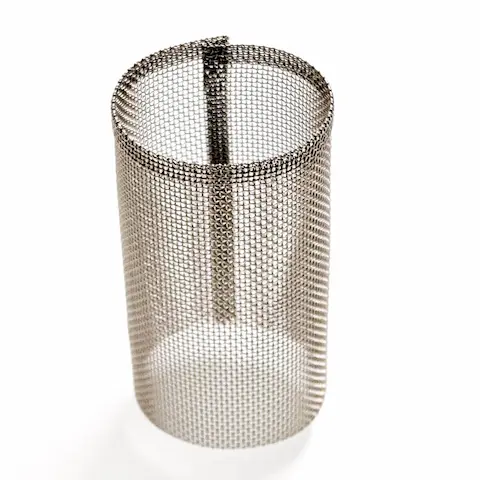